පිටකිරීමේ ක්රියාවලිය මගින් පොලිකාබනේට් (පීසී) පැතලි පත්රයක් බවට පත් වේ. නිස්සාරණ ක්රියාවලියේදී, පොලිකාබනේට් ඉහළ උෂ්ණත්වයක් හා පීඩනයක් ඇති ප්රදේශයක් හරහා ඉස්කුරුප්පු ඇණ හරහා අඛණ්ඩව තල්ලු කර එය උණු කොට සංයුක්ත කර අවසානයේදී ඩයි හැඩයකින් බල කෙරෙයි. PC විවිධ thickness ණකමකට නෙරපා හැරිය හැකිය: 0.25mm, 0.5mm, 0.7mm, 0.8mm, 1.0mm, 1.2mm, 1.5mm සහ 2.0mm. බහුලව භාවිතා වන thickness ණකම 0.5mm, 0.7mm, 0.8mm සහ 1.0mm වේ.
පරාවර්තක, ප්රතිදීප්ත, දෘශ්ය හා විනිවිද පෙනෙන බලපෑමක් ලබා ගැනීම සඳහා පරිගණකය විවිධ වර්ණක සමඟ මිශ්ර කළ හැකිය.
වයනය පළාත් සභා පත්රය නිර්මාණය කිරීම සඳහා ඉස්කුරුප්පු නියන යන්ත්රය විවිධ වයනය යෙදිය හැකිය.
Coextrusion PC / PMMA. පටල හෝ තහඩු විවිධ පොලිමර් දෙකක හෝ වැඩි ස්ථර වලින් සමන්විත වන අතර උණු කළ ධාරාවන් මිශ්ර කිරීමෙන් නිෂ්පාදනය කළ හැකිය. තනි පොලිමර් එකකින් ලබා ගත නොහැකි ගුණාංග සංයෝජනය කිරීම සඳහා ද්රව්ය ඒකාබද්ධ කිරීම සඳහා මෙම ක්රියාවලිය භාවිතා කළ හැකිය.
හිස් කබල මොළය ආරක්ෂා කරන බැවින් රික්ත සැකසීමේ පරිගණකයට බලපෑම් ආරක්ෂාවක් සැපයිය හැකිය.
භ්රමණ බලපෑම් ශක්තිය කළමනාකරණය කිරීම සඳහා MIPS ක්රියාකාරීත්වය නිර්මාණය කිරීම සඳහා රික්ත සැකසුම් පරිගණකය ස්ලයිඩින් ස්තරයක් විය හැකිය.
තර්මෝෆෝමිං යනු හෙල්මට් නිෂ්පාදනය සඳහා ජනප්රිය ක්රියාවලියක් වන අතර, එය පෙර රත් කිරීම සඳහා සිල්ක්ස්ක්රීන් වර්ණ පොලිකාබනේට් පත්රයක් උඳුන තුලට දමා, පොලිකාබනේට් රික්ත යන්ත්රයට දමා, පත්රය නම්යශීලී සැකසුම් උෂ්ණත්වයකට රත් කර, අච්චුවක නිශ්චිත හැඩයකට, විවිධ නිෂ්පාදන හැඩයට සකසා ඇත. සහ උස රික්තය සෑදීමේදී විවිධ විස්තාරණයන්ට හේතු වනු ඇත, සිහින් රික්තය පළාත් සභා විසින් වර්ණ ගැන්වීම හෝ හෙල්මට් ශක්තිය අඩු කිරීමේ වැඩි අවදානමක් ඇති බැවින් හෙල්මට් වල ගුණාත්මකභාවය හා බලපෑමට ලක්වන පරීක්ෂණයට අදාළ නිවැරදි පොලිකාබනේට් තහඩු thickness ණකම විශ්ලේෂණය කර තෝරා ගැනීම ඉතා වැදගත් වේ. භාවිතා කළ හැකි නිෂ්පාදනයක් නිර්මාණය කිරීම සඳහා කැපීම.
රික්තය සෑදීමේ ක්රියාවලියට පෙර, අපි නිස්සාරණයෙන් පසු පොලිකාබනේට් පත්රයේ ආරක්ෂිත පටල තට්ටුවක් යොදන්නෙමු, චිත්රපටය පොලිකාබනේට් ඊපීඑස් අච්චු කිරීමේදී සීරීමෙන් ආරක්ෂා කරයි, සහ අවසාන හෙල්මට් එකලස් කිරීමේදී ආරක්ෂිත චිත්රපටය ඉවත් කරන්න.
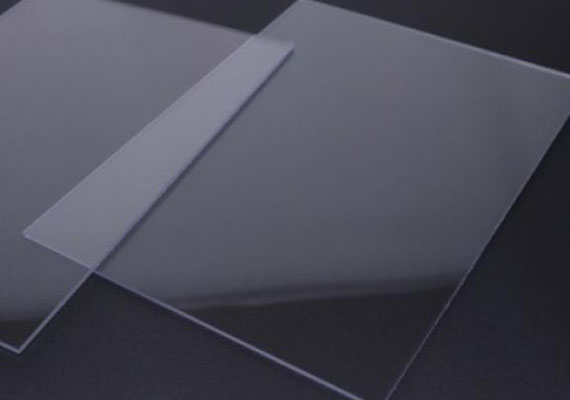
සංයුක්ත PC PMMA
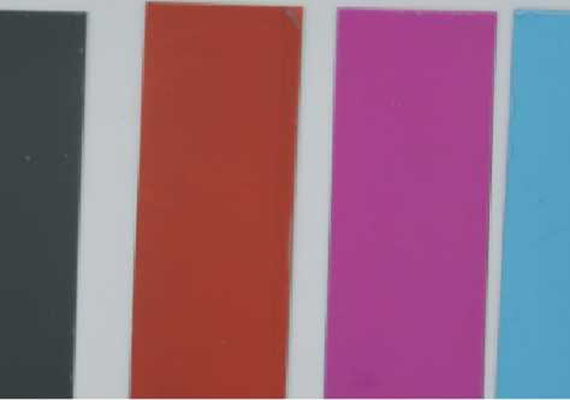
විනිවිද පෙනෙන වර්ණවත් PC
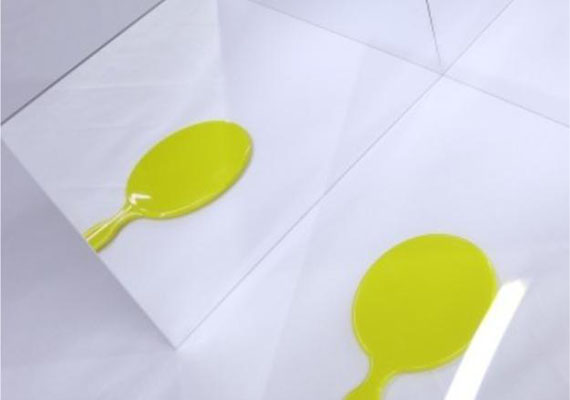
මිරර් ඔප්ටිකල් පීසී
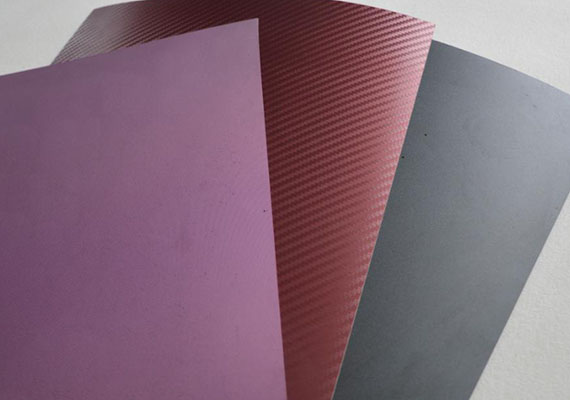
ටෙක්ස්චර්ඩ් පීසී
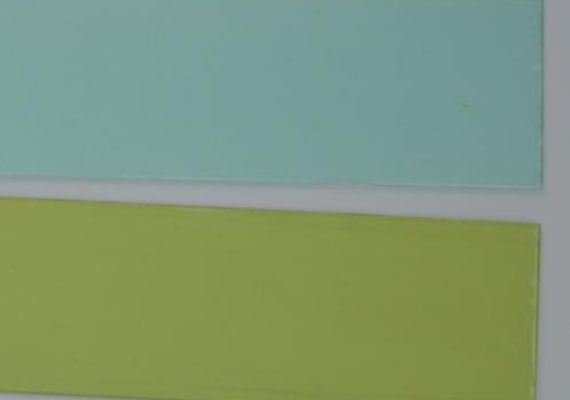
ප්රතිදීප්ත පීසී
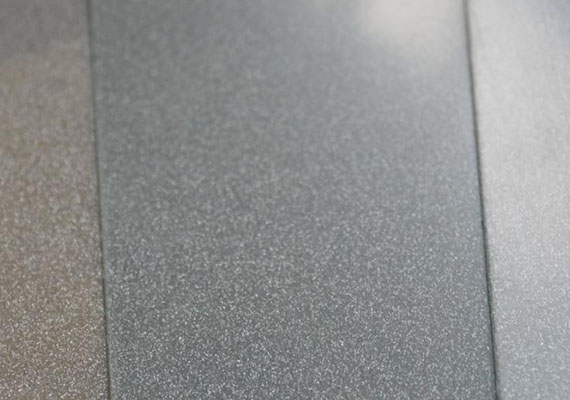